Producing high quality refractory bricks by extrusion
Cerámica Campo produces high quality refractory bricks for the heavy clay industry only by extrusion. All refractory parts are manufactured in a plastic shaping process, either by means of plain extrusion or extrusion plus re-pressing.
Various refractory chamottes combined with suitable proportions of our own refractory clays and additives produce a wide range of mixes with varying degrees of thermal shock resistance and refractoriness with an operating temperature of up to 1,400 °C (2,552 °F).
Our special manufacturing process includes several phases, each of which includes a raw material or innovation that sets our product above from the rest.
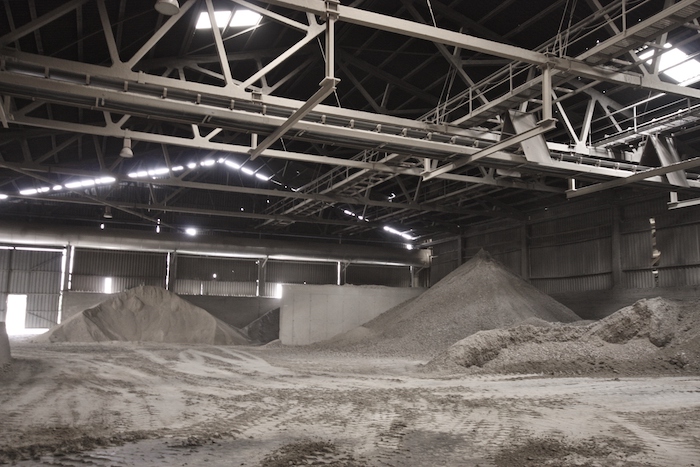
- Clay grinding Dosing. Mixing. The various raw materials (cordierite clay, chamottes and additives) are dried, dry grounded and dosed gravimetrically, using automatic and precision systems.
- Kneading Automatic humidity regulation and pre-extrusion.
- Molding We manufacture hollow refractory pieces by extrusion in high performance vacuum biscuits, in low humidity and high-pressure conditions, which guarantee excellent compactness and measurement stability.
- Drying We use dryers with independent chambers, which allow for isolated drying cycles for each piece series. Cerámica Campo uses robot feeding systems and precision sensors for monitoring. Reducing humidity is a lengthy process, involving exhaustive controls, temperature and time, depending on the shape and size of each piece model.
- Firing The pieces are fired at temperatures of up to 1,400 ºC (2,552 °F) in our own unique kiln, designed especially for refractory forms. High-tech software controls all the many variables that come into play in the process and determines the quality of the end products.
- Cutting and grinding The cold pieces are ground longitudinally to their exact size using an automatic cutting and diamond disc system.
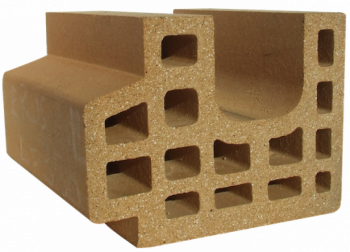
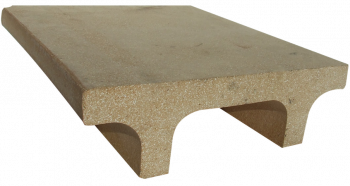
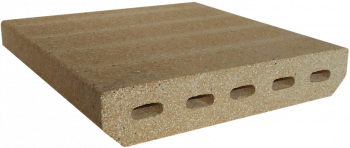
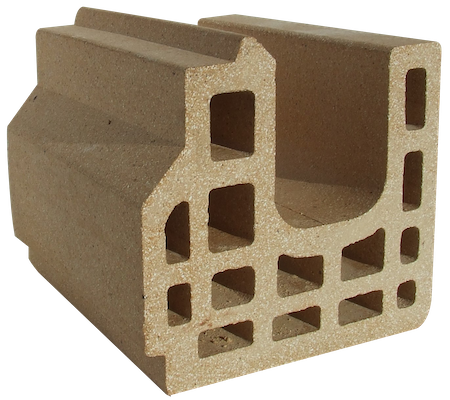
Advantages of extrused refractory linings
Our process has a number of technological advantages over dry pressing in molds and wet milling. Cerámica Campo can produce a wide range of shapes, including three-dimensional and hollow options, an excellent basis for innovative designs.
Energy saver
Lighter linings and hollow shapes allows for lower energy consumption by improving the firing cycle with lighter cars.
Resistance
Improved thermal shock resistance, based on a high percentage of cordierite mineral, plus a very low percentage of free quartz.
Flexibity
Extrusion allows for flexibility in the design of unique pieces them without expensive costs. Cerámica Campo has delivered more than 500 references worldwide.
Accuracy
Dimensional accuracy is achieved by the strict control of the mixing and manufacturing parameters, completed by diamond cutting of all pieces to an exact length.
High density
The dry mill produces very small particles. Fewer and smaller pores guarantee efficiency against chemical attack, which is especially relevant when alkali-containing clays and/or aggressive fuels are used.
Heat transfer
Faster heating up and cooling down of the refractory parts in contact with the ceramic ware, resulting in better heat transfer and improved quality of the final product (bricks or tiles).
Thickness
Compactness and strength are not affected by differences in thickness of the refractory pieces. The forming process is highly isostatic due to the flow capacity of the plastic body.
Grinding facilities
Grinding facilities are used when extreme precision and/or flatness is required, as is the case for large-size setting supports or supporting parts for U or H setters.
Contact us
If you have specific questions and would like to reach one of our engineering specialists directly, please use our contact form on this site.
We will be pleased to help you!