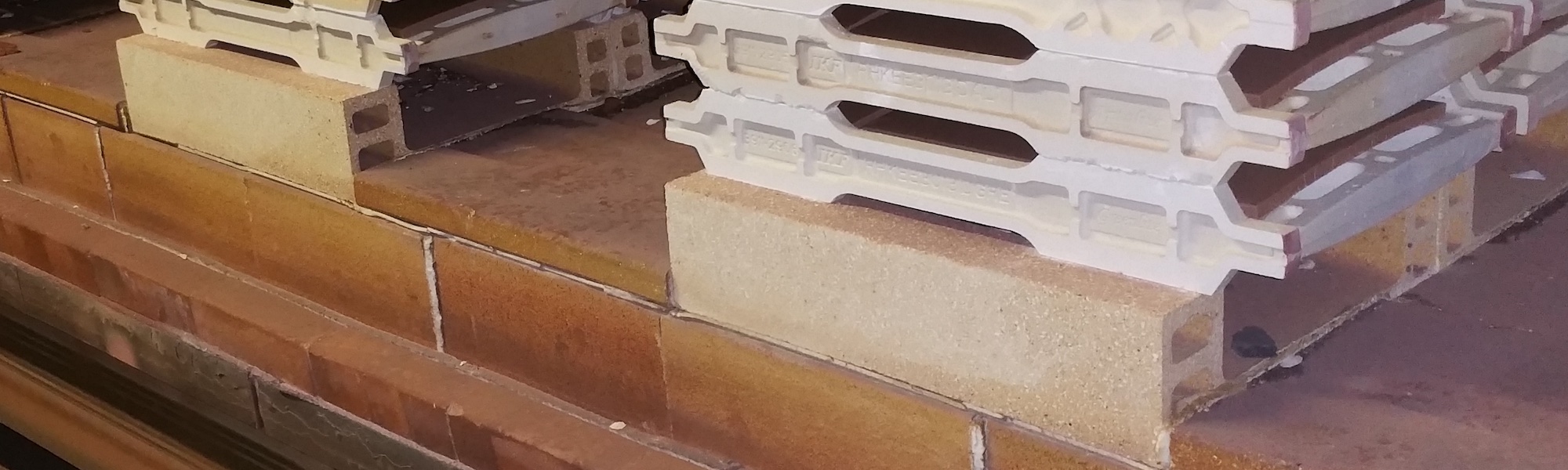
Tunnel kiln car for firing tiles in H-Cassettes
Overview
Producing tiles in H-cassettes is the most effective system for high quality roofing tiles. It ensures high temperatures and fast-firing of roof tiles. The kiln car, due to the constant heating and cooling, is the tunnel kiln component most exposed to severe stresses.
Cerámica Campo and Forgestal (engineering partner) meet the needs with specific made-to-measure kiln cars for H-cassettes, with high quality refractory linings.
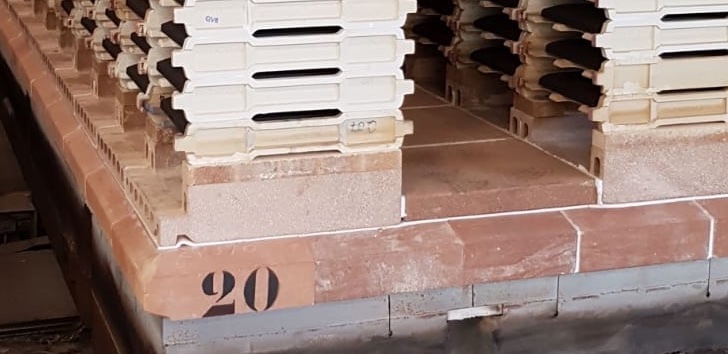
Challenges
The kiln cars for roofing tiles loaded on H-shaped refractory cassette give the final product high quality. Individual curing of each piece provides excellent flatness, allows all kinds of surface treatment (powder, glaze or engobes) with no contact points.
The production ranging per day is very high because of automation of the handling process of roof furniture (H-cassettes) and the homogeneous firing thanks to the tight control of airflow inside the kiln.
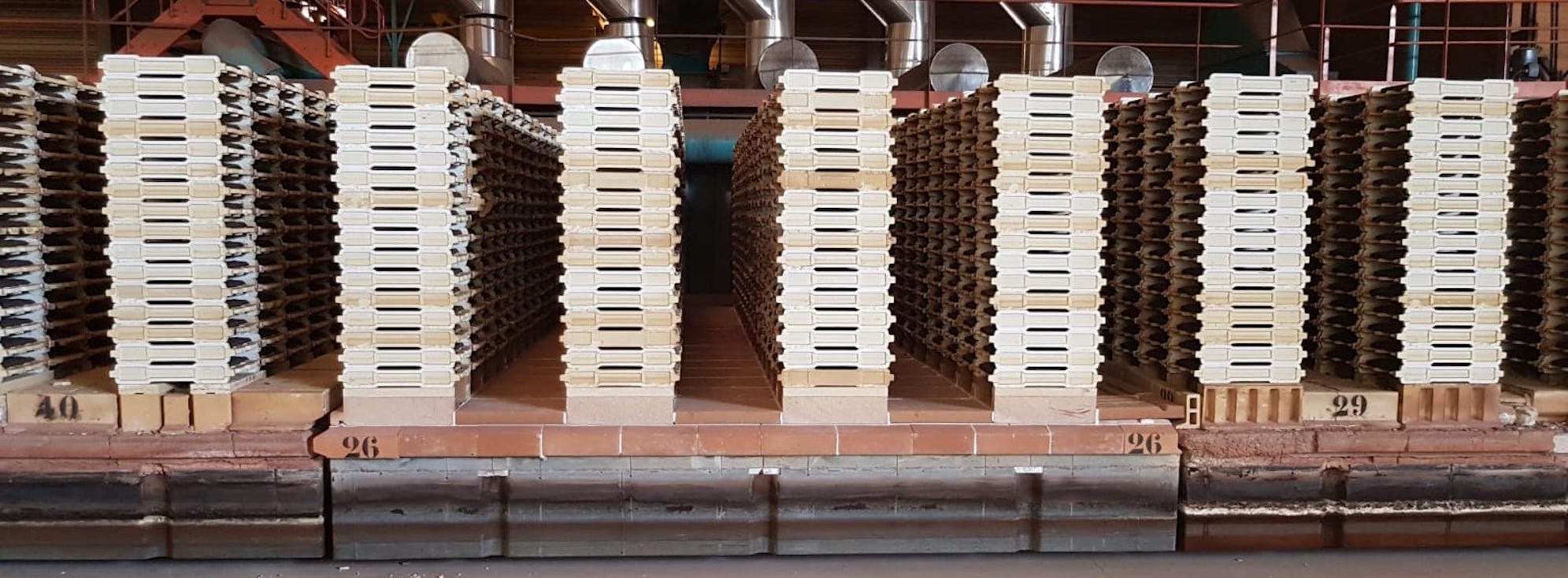
Materials and design have a deep impact on the durability of H-cassettes and on energy consumption. There are two major challenges in the design and production of cars:
- H-cassette tunnel kilns work in very short cycles for compensate the low load density (roofing tiles/car) and taking advantage of the fact that the overall load is highly ventilated. The short cycles leave little time to cool down the car and recover stored energy before the car leaves the tunnel.
- Increased wear of kiln furniture, and its cost, is a pain point for this fire method. Due to thermal expansion of the H-cassettes inside the kiln, friction damages the lower supports in contact with the refractory setters on the superstructures. The reasons are, firstly, coefficients of thermal expansion that differ from those of the cassette material. Secondly, the left and the right feet of the H-cassette stack are usually each placed on separate support elements, which has the effect that during the heating and cooling operation the changes in length are in opposite directions, resulting in high frictional forces. This stress occurs during each cycle and the feet are liable to spall, or chip.
Solution
Cerámica Campo and Forgestal (engineering partner) design and produce the kiln car as a complete system with patented setting supports for H-cassettes. Our solution is based on:
- Reduction of the fire car weight using hollow bricks and refractory aggregates (siliceous and aluminous) results in less mass to be heated and cooled.
- Patented H-cassette support four-feet-on-one-support. All four feet of the lower setter are supported on a single, precision-ground, refractory piece.
- Made-to-measure bricks. Our system allows for flexibility in the design of singular pieces for every single customer at an affordable cost.
- High quality refractory linings with mixes composed of refractory chamotte, refractory clays and additives.
- Mechanical grinding for extreme accuracy and/or flatness requirements.
The design, supply and assembly of chassis can also be offered as a part of a complete turnkey service. For existing kiln cars, new linings can replace the old ones partially or progressively.
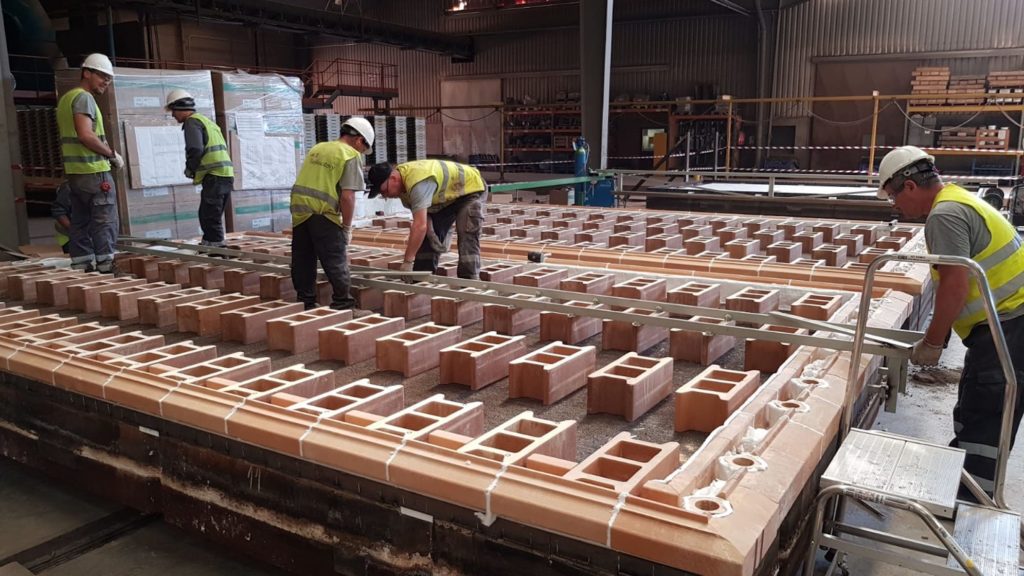
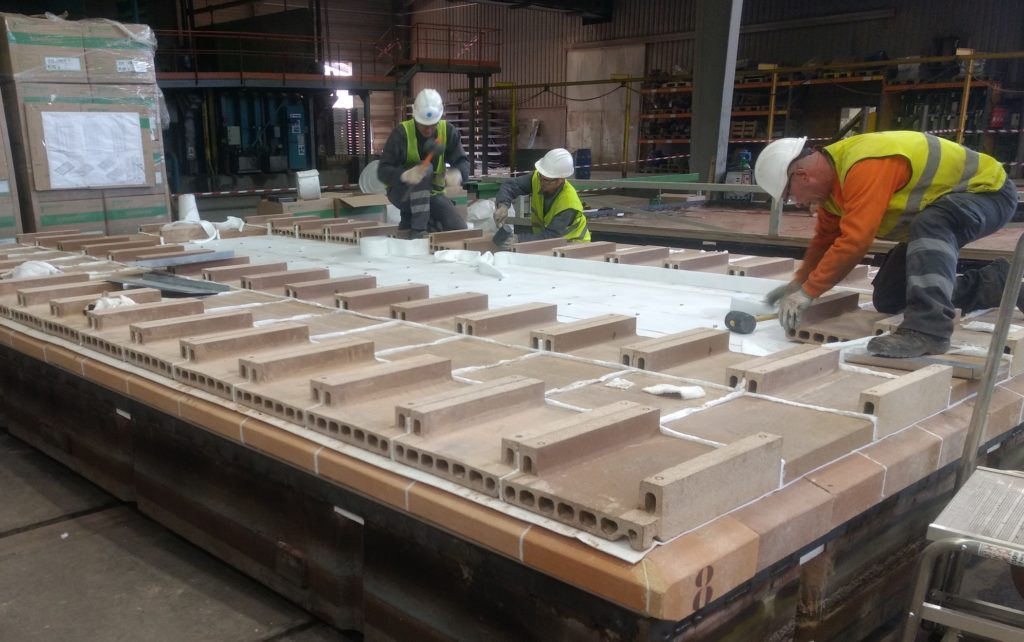
Refractory hollow bricks
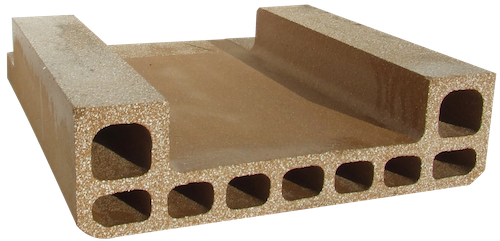
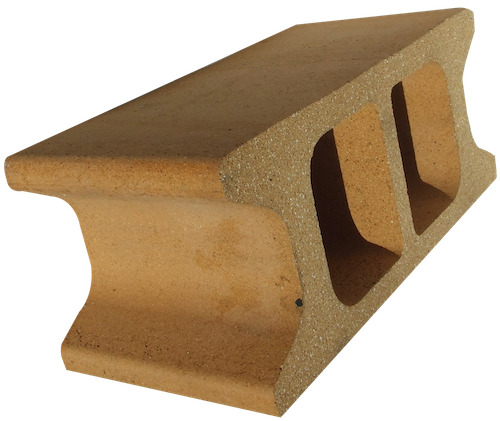
Result
The kiln car matches the criteria of any clay industry focused on producing high quality roofing tiles. Any plant with our solution gets:
- Faster heating up and cooling down of the kiln car system, resulting in higher energy efficiency and better quality of the fired roofing tiles.
- Shortening of the firing cycle and therefore higher output of tiles/day.
- Our patented support provides a completely flat surface for the H-cassette to sit on. Reduced mechanical twisting of the load on the setter. The operator benefits from a lower breakage rate and therefore from a longer lifetime of the setters.
- No base frames for the underfloor ventilation are required. H-cassettes can be stacked directly onto the car.
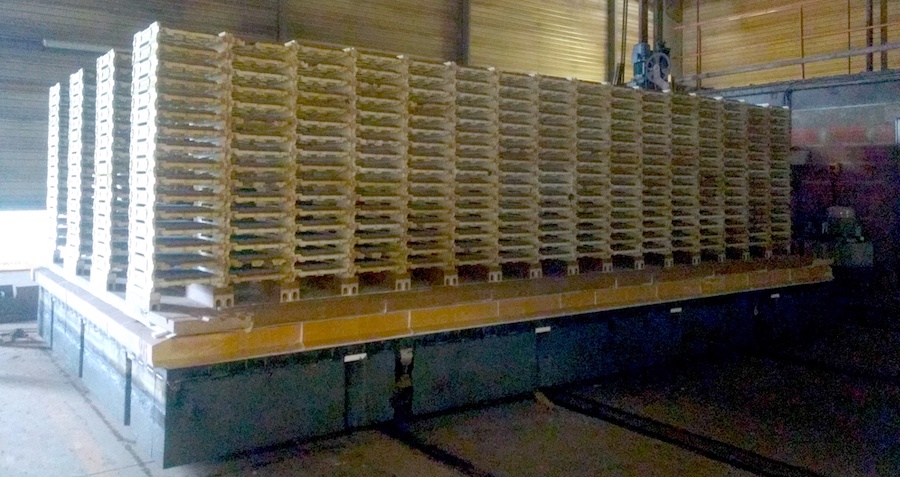
Additional advantages are:
- Less CO2 emission rights to be purchased.
- Lower maintenance costs.
Disclaimer: Every plant and every thermal process is different. Static, dynamic and thermal conditions require the selection of the appropriate design and refractory material.
Contact us
If you have specific questions and would like to reach one of our engineering specialists directly, please use our contact form on this site.
We will be pleased to help you!